How to optimise maintenance with Dupont ™ MOLYKOTE® lubricants.
To ensure optimum lubrication and prevent failure, it is absolutely crucial to prepare the surface of materials thoroughly and properly before applying the lubricant.
Samaro and its partner Socomore recommend the use of Diestone DLS. This chlorinated hydrocarbon-free cleaner and degreaser evaporates quickly, ensuring perfect surface preparation for effective lubrication.
In the field of industrial maintenance, lubrication plays an often underestimated but crucial role in guaranteeing optimum performance. As well as reducing friction, effective lubrication is essential to ensure the efficiency, reliability and durability of industrial equipment.
The importance of lubrication in maintenance
Lubrication in the context of maintenance involves much more than the application of oils or greases to ensure smooth operation. Good lubrication improves overall efficiency and extends the life of machinery. Lubrication performance depends on the quality and specific characteristics of the lubricant chosen. Good machine operation is essential for productivity and to minimise downtime. Lubrication prevents metal parts from rubbing against each other, reducing wear and tear. It also removes impurities that can damage vital components, preventing costly operational breakdowns.
The crucial choice of lubricants
Selecting the right lubricant is essential for effective maintenance. A high-quality lubricant that complies with recommended standards ensures optimum performance and long machine life. Conversely, a poor-quality lubricant can increase friction, generate excessive heat and cause deformation during operation, compromising machine efficiency and leading to additional maintenance costs.
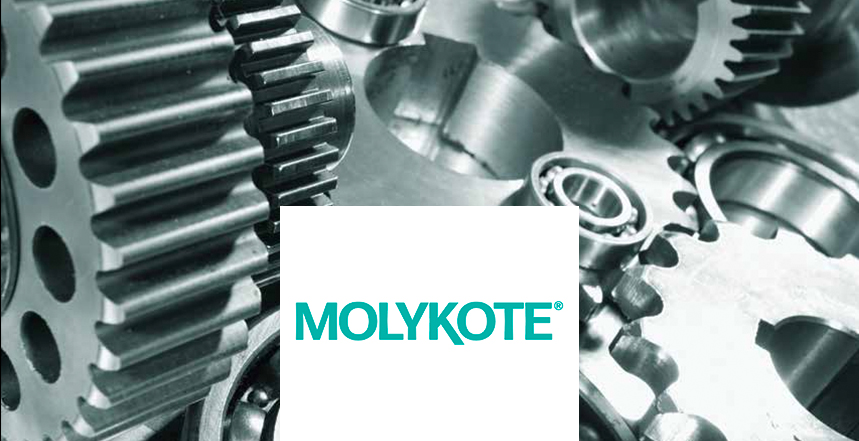
MOLYKOTE®: A leader in lubrication
With over 75 years’ experience, MOLYKOTE® offers first-class lubrication solutions. Their product range is specifically designed to meet the diverse needs of industrial maintenance operations, offering high quality lubricants suitable for a multitude of applications.
Some examples of MOLYKOTE® products:
MOLYKOTE® 1000 :
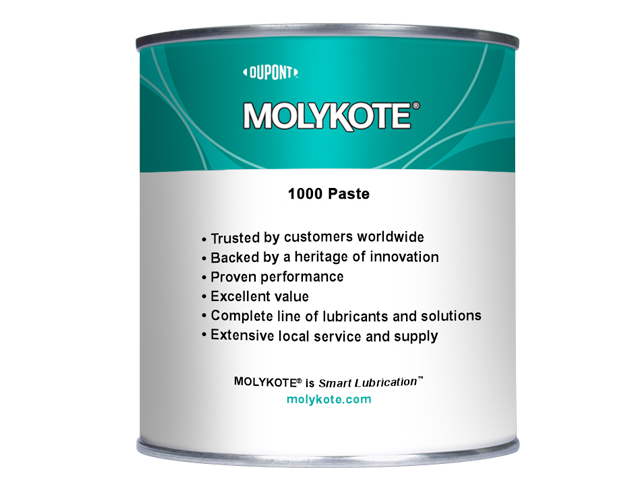
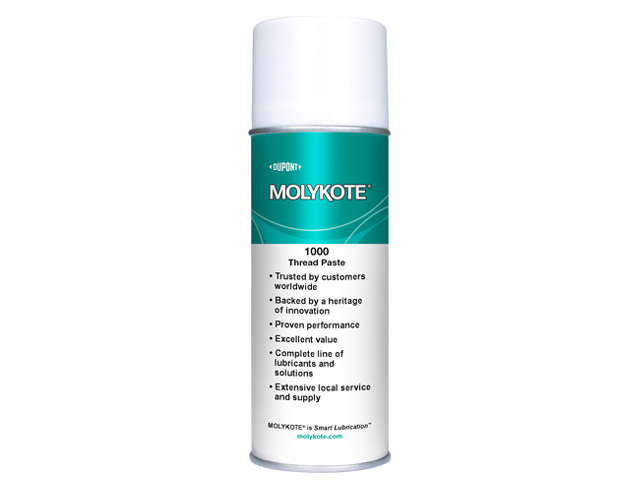
Application : Copper paste for high-temperature screwed assemblies (up to 650°C). Ideal for metal-to-metal applications, it protects against corrosion in threaded connections, splined shafts and other areas subject to high pressure.
Also available in spray.
MOLYKOTE® MULTILUBE :
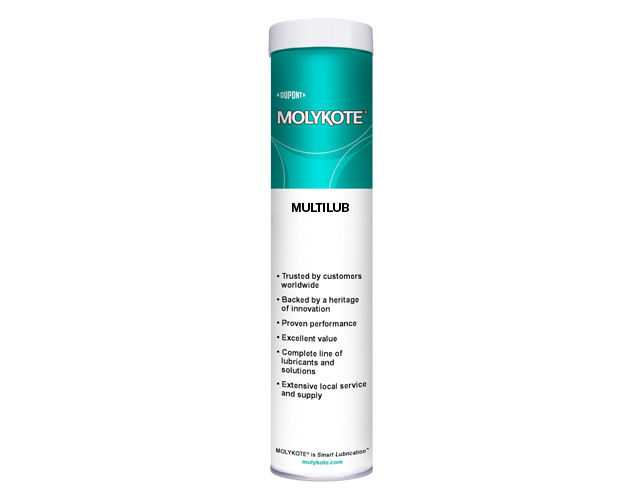
Application : Suitable for contacts subjected to medium loads at medium speeds in humid environments. Used to lubricate plain bearings, roller bearings and other components in a variety of industries.
MOLYKOTE® BR2 PLUS :
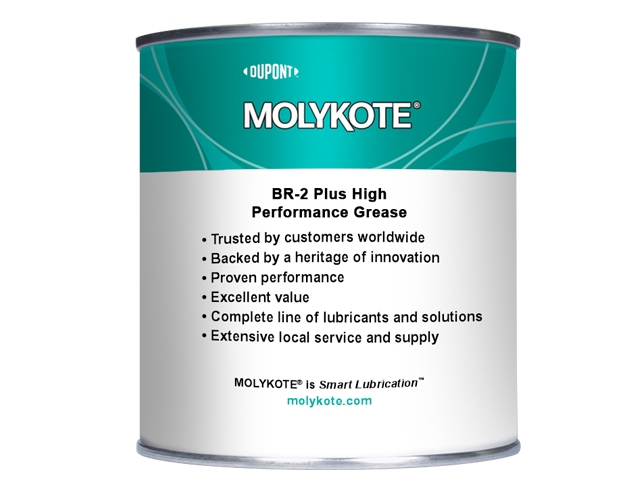
Application : Grease for bearings, plain bearings, guide rails and other industrial applications. It resists water washing and protects against rust and corrosion.
MOLYKOTE® D-321 R :

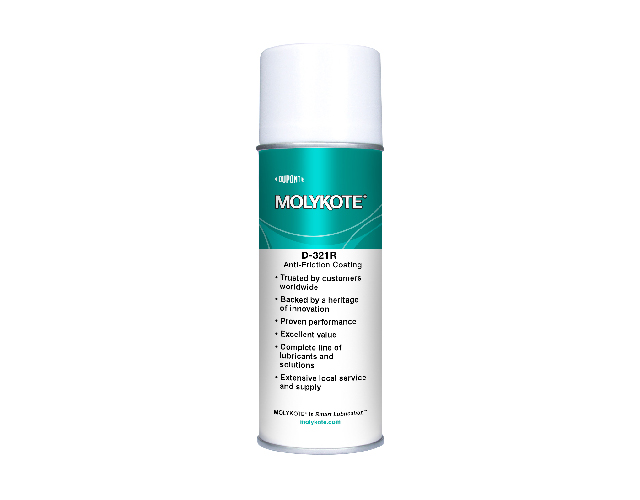
Application : Anti-friction coating for medium-speed metal/metal combinations under heavy loads, permanent lubrication of guideways subject to low speeds and intermittent movements.
Also available in spray.
MOLYKOTE® G-N PLUS :
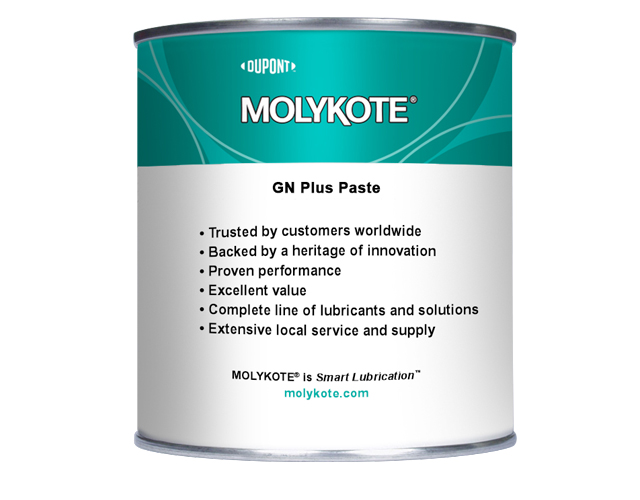
Application : Lubrication and protection of metal parts during assembly, fitting and lapping to prevent galling and fretting corrosion in threaded connections and sliding surfaces.
Lubricant selection requirements
To select the appropriate MOLYKOTE® products, it is essential to consider the characteristics of the lubricant in relation to the specific requirements of the equipment, including load, speed, temperature and environmental conditions.
Please visit the MOLYKOTE® product pages where you will find technical data sheets and safety data sheets in the download section. You can also contact our technical department for personalised advice on your application.
Explore MOLYKOTE® specialist lubricants
DuPont™ MOLYKOTE® brand specialty lubricants provide solutions for the oil and gas industry worldwide. Their wide range of products and service and support capabilities help you solve or prevent even the most complex lubrication problems.