Optimising valve lubrication and sealing for oil and gas applications.
To ensure optimum lubrication, it is crucial to carefully prepare the surface of materials before application.
With this in mind, Samaro and its partner Socomore recommend using Diestone DLS. This chlorinated hydrocarbon-free cleaner and degreaser evaporates quickly, ensuring ideal surface preparation for effective lubrication.
Discover MOLYKOTE® Smart Lubrication™, the established solution to a multitude of valve challenges. These high-performance solutions include anti-seize pastes, anti-friction coatings, lubricating greases and silicone compounds. Designed to withstand heavy loads, extreme temperatures and corrosive environments, these lubricants meet the specific needs of valve components.
Ensuring reliable, leak-free operation is essential in the oil and gas industry for reasons of safety, loss prevention and environmental protection. Different types of valves, such as ball, knife, butterfly and wedge valves, are used as control valves, requiring precise and repeatable responses. Whether in production, transportation or processing, these valves must deliver consistent performance, often in harsh environments: handling materials under pressure, exposure to extreme temperatures, and sometimes prolonged inactivity.
Valve problems caused by inadequate lubrication and sealing, abrasive contaminants or heavy use can result in seizure, seal or gasket failure, corrosion and internal and external leakage.
Correct lubrication of valve components is therefore crucial to reducing wear, improving durability and reliability, and ensuring the safe and efficient transport of pipeline contents. It also preserves valve seals, inlets and packing materials, ensuring leak-free operation.
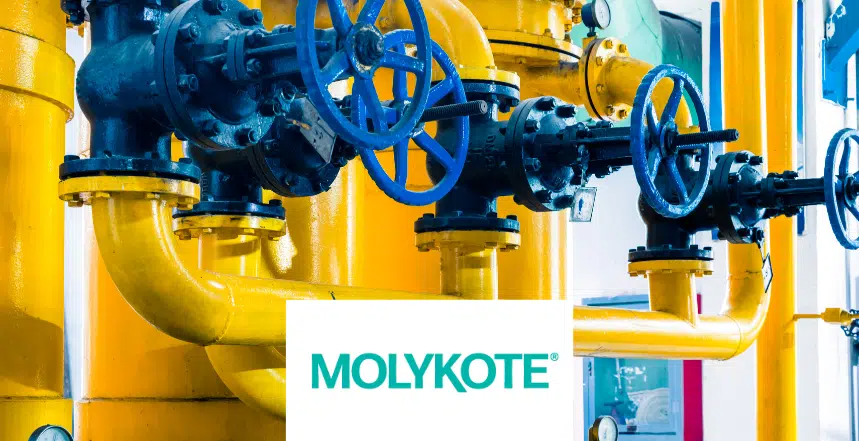
MOLYKOTE® Smart Lubrication™ solutions for valve components:
Application / Product | Description |
Packings and Seals | |
MOLYKOTE® 111 | Silicone avec épaississant inerte, compatible avec de nombreux élastomères. Sert de lubrifiant et de produit d’étanchéité non durcissant dans une large gamme de températures. |
Bearing seal and sealing groove (to hold the seal) | |
MOLYKOTE® CU-7439 PLUS V1 MOLYKOTE® CU-7439 PLUS V1 SPRAY |
Copper-based solid lubricants, excellent adhesion to metals, resistant to water washout, good corrosion protection, from -30°C to +300°C up to +650°C in dry lubrication, low evaporation – No dropping point. |
Seal sliding surfaces, sealing ring | |
MOLYKOTE® D-321R MOLYKOTE® D-321R AEROSOL |
Air-curing MoS2-filled dry sliding varnish, rapid curing at room temperature, protection against chatter, high resistance to ageing. |
Shaft and stem |
|
MOLYKOTE® U-N | Solid lubricants in PAG oil, good compatibility with rubber, anti-friction coating for extreme heat under heavy loads. |
MOLYKOTE® 106 | Solid lubricants in a solvent resin, high load-bearing capacity, heat-hardens to form a bonded film. |
MOLYKOTE® 3402-C Lead Free | Solid lubricants in an organic solvent-based binder, resistant to high pressure and wear, protects against corrosion. |
Ball surface | |
Pâte Molykote® G | Solid lubricants in a mineral oil, prevents seizing, grooving, suppresses adhesive sliding and corrosion, ability to absorb high pressures. |
Bearings (bearing wear surfaces) | |
MOLYKOTE® 33 Light | Silicone oil with lithium soap thickener, low torque for extreme cold starts, wide operating temperature range, resistance to oxidation, moisture and corrosive atmospheres. |
Threaded connections (studs, bolts, caliper nuts, screws) | |
MOLYKOTE® Revêtements antifriction | Solid lubricants in a solvent-resin system, applied to clean, dry assembly parts, with air and heat cure options for long-term dry film lubrication. |
MOLYKOTE® P-1900 FM ANTI-SEIZE PASTE MOLYKOTE® P-1900 FM ANTI-SEIZE PASTE SPRAY |
Solid lubricants in a synthetic/mineral oil, applied in the field with aerosol options, resistant to water washout and corrosion, facilitating non-destructive assembly and disassembly. |
Body seat | |
MOLYKOTE® D-321R MOLYKOTE® D-321R AEROSOL |
Air-curing MoS2-filled dry sliding varnish, rapid curing at room temperature, protection against chatter, high resistance to ageing. |
In a real-world application, gate valves used to block or restrict the flow of raw or processed materials face challenges. Mineral oil-based grease, when exposed to aggressive pipeline materials, hardens and makes valve operation difficult, leading to leakage beyond the valve seat and seals. The solution is MOLYKOTE® 111, which maintains reliable lubrication under extreme conditions, ensuring smooth valve operation and long-term sealing integrity.
The integration of Molykote® Smart Lubrication™ solutions offers a comprehensive approach to improving valve performance and longevity in oil and gas applications. These proven solutions contribute to the industry’s safety, reliability and environmental responsibility.