What adhesive should I use to bond ABS?
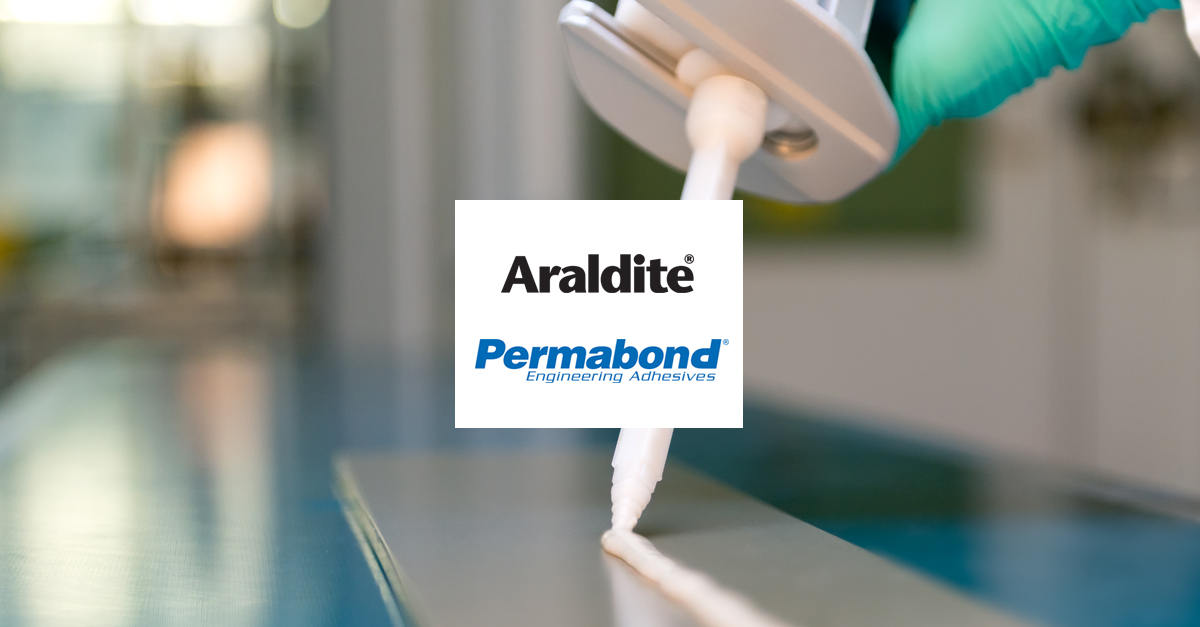
Acrylonitrile butadiene styrene (ABS) is an opaque thermoplastic polymer used in injection moulding and 3D printing applications.
ABS is made up of varying proportions of three monomers; acrylonitrile, butadiene (rubber) and styrene combine to give ABS its distinctive properties. Acrylonitrile offers good chemical resistance and thermal stability, butadiene provides impact resistance, while styrene adds rigidity and a glossy finish to the plastic.
How do you bond ABS, and what adhesives do you use?
ABS has proved to be a popular material in manufacturing due to its low production cost, ease of machining and ease of recycling compared to other plastics commonly used in engineering.
ABS can also be combined with other materials to add properties such as flame resistance and heat dissipation.
Products made from ABS include automotive dashboards, instrument panels, covers for industrial machinery, protective equipment such as helmets, medical supplies and panels for refrigerators.
Main properties of ABS
- Surface energy: 42mJ/m².
- Maximum service temperature: 89°C
- Melting temperature: 100°C
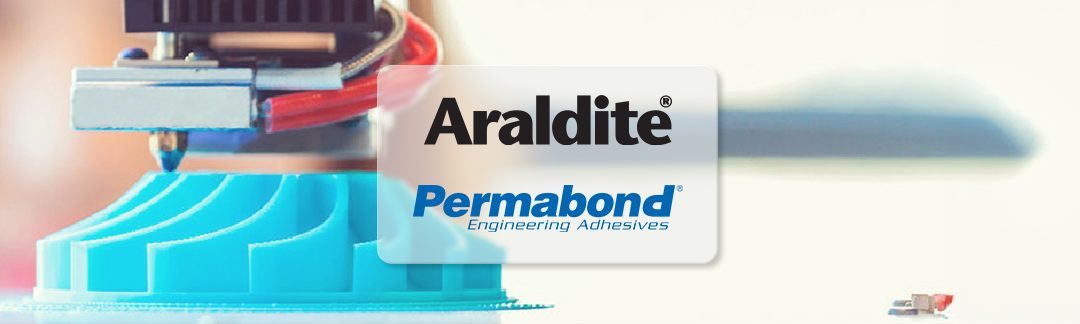
Adhesives for bonding ABS
Most adhesives, such as cyanoacrylates, two-component epoxies, structural acrylics and polyurethanes, are suitable for bonding ABS. MSP or silicone adhesives can also be used where a flexible solution is required. UV-curing adhesives can also be used to form strong bonds with ABS, provided light can reach the joint.
One way of choosing the most appropriate type of adhesive to bond ABS to is to look at the solvent or temperature resistance required for its application.
The tables below provide a guide to adhesives for bonding ABS.
Solvent resistance :
Adhesive technology | Resistance to polar solvents, e.g. water, ethylene glycol, isopropanol, acetone |
Resistance to apolar solvents e.g. motor oil, diesel, toluene |
---|---|---|
Anaerobic glue | Very good | Very good |
Cyanoacrylate glue | Poor | Good |
One-component epoxy | Very good | Excellent |
Two-component epoxy | Very good | Very good |
Modified epoxy | Good | Very good |
MS Polymers | Good | Average |
Polyurethanes | Good | Average |
Acrylic No Mix | Good | Good |
Methacrylate adhesive | Good | Good |
UV adhesive | Good | Good |
Temperature resistance :
Adhesive technology | Standard adhesive | High temperature adhesive |
---|---|---|
Anaerobic glue | 150°C | 230°C |
Cyanoacrylate glue | 90°C | 250°C |
One-component epoxy | 180°C | 300°C |
Two-component epoxy | 80°C | 180°C |
Modified epoxy | 80°C | – |
MS Polymers | 100°C | – |
Polyurethanes | 90°C | – |
Acrylic No Mix | 150°C | 230°C |
Methacrylate adhesive | 120°C | 150°C |
UV adhesive | 120°C | 150°C |
Surface preparation tips for ABS
To ensure an effective bond, it is vital to prepare the surface of the materials to be bonded meticulously before any application.
Surfaces must be clean, dry and free from contamination.
With this in mind, Samaro and its partner Socomore recommend the use of Diestone DLS. It is a chlorinated hydrocarbon-free cleaner and degreaser that evaporates quickly, providing ideal surface preparation for effective bonding.