How to lubricate a plastic and elastomers parts ?
Lubricate plastic and elastomer components (EPDM o-ring seal)
Lubrication of plastic and elastomer parts such as EPDM o-ring seal, oven or autoclave seal, POM plastic gear, PC-looking parts, kinematic system in PA6.6. etc… must be considered on a case-by-case basis. It is essential to take into account the possible interactions between the materials and the lubricant used (metal/plastic, metal/elastomer or plastic/elastomer).
In this context, the use of specific lubricants such as those supplied by the Molykote and Krytox brands can be particularly beneficial in ensuring effective, long-lasting lubrication while preserving component integrity.
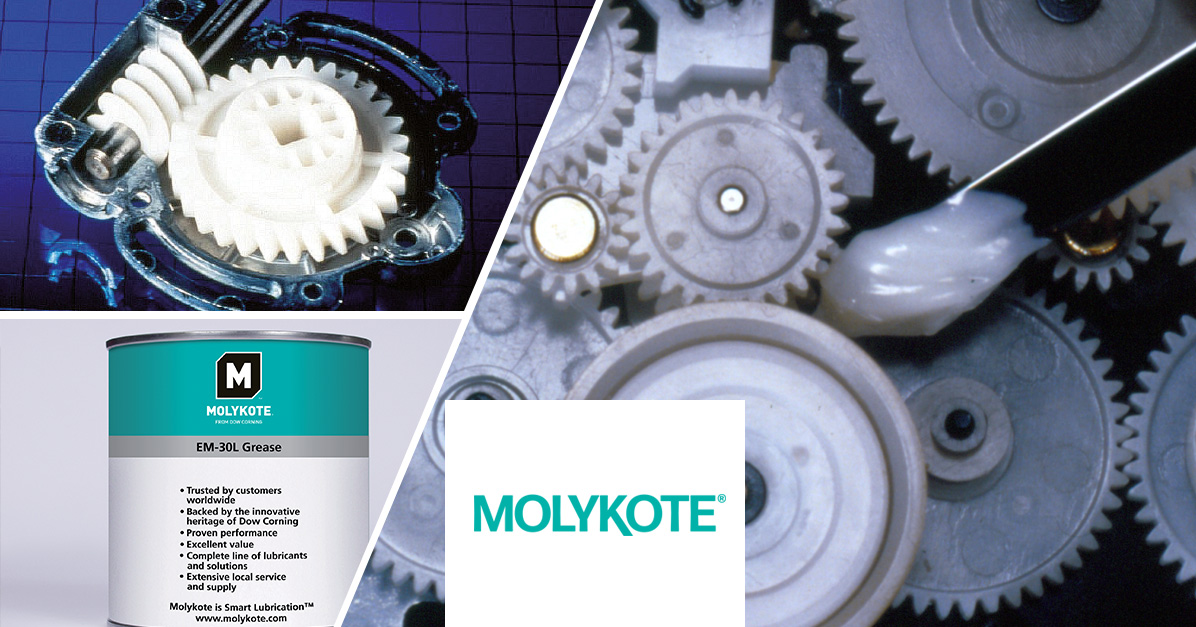
An unsuitable lubricant can cause :
- a swelling or shrinkage of the synthetic materials which can lead to leaks or even leakage.
- stress-cracking (material embrittlement leading to the start of breakage within the material) of plastic materials.
- A change in the elastic properties.
To ensure compatibility, SAMARO has feedback on the materials and base oils used. We usually complete with an accelerated ageing test by placing the material in contact with the lubricant in an oven at 80°C for 7 days and assessing the weight loss/gain and visual changes in the material.
References | Temperatures | Load | Features | Properties |
---|---|---|---|---|
Heavy loads applications |
||||
Molykote™ YM-103 | 45°C +120°C up to 150°C peak | 4800 N | PAO – Lithium – Solid lubricants – Yellow – NLGI 1-2 | Very heavy loads – Wide temperature range – Long-lasting lubrication due to low tendency to oxidation – Low starting torque – Excellent water resistance |
Applications for métal / plastique |
||||
Krytox® GPL 205 | -36°C +204°C | NC | PFPE – PTFE – NSF-H1- Base oil at 40°C (104°F): 160 cSt | High temperature grease – Compatible with all plastic and elastomer materials |
Molykote™ G-4500 FM | -40°C +150°C | 3100 N | PAO – PTFE – White – NLGI 2 NSF-H1 | Excellent lubricant properties – Good load bearing capacity – Wide temperature range |
Molykote™ G-807 | -40°C +150°C | NC | Silicone (high viscosity = 22500 cSt to 40°C) – PTFE – Blanche – NLGI 1 | Low coefficient of friction silicone compound – Compatible with many plastics and rubbers – Wide range of operating temperatures – Good corrosion resistance – Low coefficient of friction |
Molykote™ PG-75 | -40°C +130°C | 1300 N | Semi-synthetic – Lithium – Solid lubricants – Beige – NLGI 2 | Metal/plastic combination – Long-lasting lubrication – Good behaviour at low temperatures – Very low coefficient of friction |
Molykote™ G-2003 | -50°C +150°C | 2200 N | PAO – Lithium – Solid lubricants – Beige – NLGI 2 | Long-lasting grease – Very good behaviour at low temperatures – Good water resistance |
Low coefficient of friction |
||||
Molykote™ EM 30L | -45°C +150°C | 3800 N | PAO – Lithium – PTFE – Solid lubricants – White – NLGI 1 | Heavy-duty grease – Wide temperature range – Long-lasting lubrication – Low coefficient of friction |
Molykote™ EM 50L | -40°C +150°C | 1400 N | PAO – Lithium – White – NLGI 1 | Noise reduction – Wide temperature range – Improves adhesion to surfaces |
Molykote™ G-1067 | -50°C +120°C | 1900 N | PAO – Solid lubricants – White | Maintains a very low friction coefficient even after contamination (dust, sand,…) – Does not stain textiles – Reduces operating noise – Very good lubrication of the POM |
Molykote™ PG-54 | 50°C +180°C | 2000 N | Silicone – Lithium – White – PTFE – NLGI 2-3 | Wide temperature range – Low coefficient of friction – Excellent protection against corrosion and oxidation |
Contact plastic/ plastic |
||||
Molykote™ PG-65 | -55°C +130°C | 2100 N | PAO – Lithium – Solid lubricants – White – NLGI 2 | Compatible with many plastics – Low coefficient of friction – Designed for high speed applications |
Molykote™ PG-21 | -50°C +190°C | 1600 N | Silicone – Lithium – White – NLGI 2 | Wide temperature range – High resistance to oxidation – High resistance to water – Excellent corrosion protection |
Molykote™ G-1057 | -50°C +150°C | 1400 N | PAO – Transparent | Reduces oil separation – Reduces contamination and is non-staining on textiles – Reduces operating noise |