Maximize the Reliability and Durability of Your Wind Turbines with MOLYKOTE® Lubricants
Wind energy is a cornerstone of renewable energy, with efficiency continuously improving to meet the growing global demand for electricity. Proper lubrication plays a key role in this evolution, ensuring the reliability, efficiency, and reduced operational costs of wind turbines. MOLYKOTE® Specialty Lubricants deliver high-performance solutions tailored to the unique needs of wind turbine components, providing superior results and supporting sustainability.
In this article, we’ll explore why MOLYKOTE® is the preferred choice for wind turbine lubrication and how these solutions can enhance turbine performance while achieving your sustainability goals.
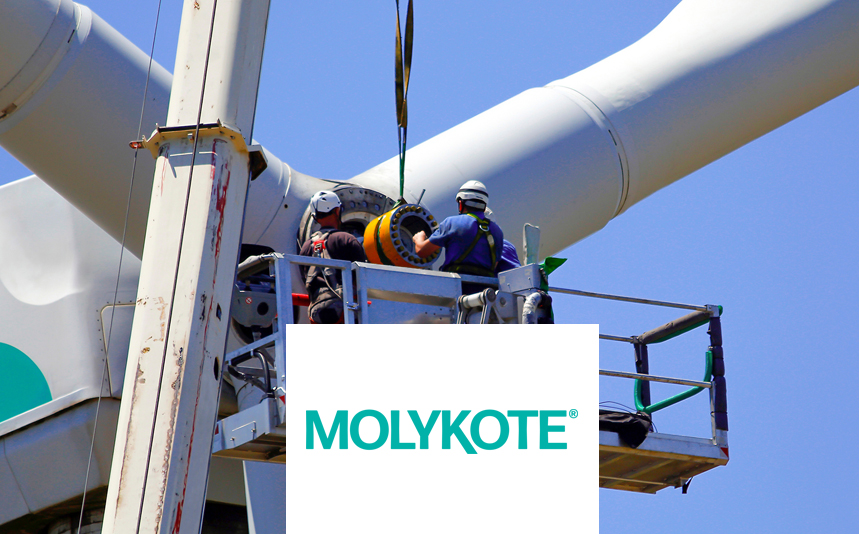
Optimized Lubrication for Key Wind Turbine Components
Wind turbines operate under extreme conditions: strong winds, heavy loads, and temperature fluctuations. Each component requires special attention to ensure seamless operation. Here’s how MOLYKOTE® lubricants are revolutionizing wind turbine maintenance:
1. Threaded Connections
Threaded connections must handle high torque and resist environmental challenges like corrosion. MOLYKOTE® 1000 Paste and MOLYKOTE® G-Rapid Plus Paste provide:
- Consistent Friction Performance: Reliable friction over multiple assembly and disassembly cycles.
- Seizing Prevention: Protection against galling and wear.
- Corrosion Resistance: Extends the life of threaded components with advanced anti-corrosion properties.
2. Pitch and Bushings
Pitch and bearings, essential for blade movement, require robust lubrication. MOLYKOTE® Longterm 2 Plus Grease delivers:
- Smooth Operation: Ensures durable, frictionless performance.
- High Load Capacity: Handles extreme pressure and protects bearings from damage.
- False Brinelling Prevention: Protects against wear caused by vibrations.
3. Shrink Discs
Shrink discs, crucial for torque transmission, benefit from MOLYKOTE® D-321 R and MOLYKOTE® 1000 Paste:
- Lifetime Lubrication: Durable performance under demanding conditions.
- Wear Reduction: Protection against friction and wear, simplifying maintenance.
- Fretting Protection: Prevents damage caused by micro-movements.
4. Yaw Brake Systems
Yaw brake systems, responsible for turbine positioning, require precision and durability. MOLYKOTE® 3402-C LF Anti-Friction Coating ensures:
- Noise Reduction: Minimizes operational noise for smoother performance.
- Extended Lifespan: Reduces wear for prolonged functionality.
5. High-Voltage Connectors
Protecting high-voltage connectors is essential to avoid power disruptions. MOLYKOTE® 111 Compound offers:
- Moisture Sealing: Prevents water ingress and corrosion.
- Electrical Stress Resistance: Handles extreme electrical demands.
- Simplified Assembly: Eases installation and maintenance processes.
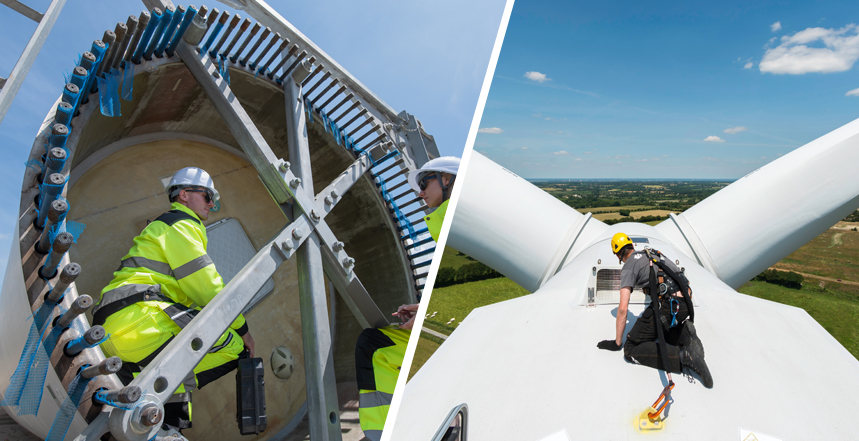
Why Choose MOLYKOTE® Specialty Lubricants for Wind Turbines?
MOLYKOTE® has been a trusted brand for over 75 years, recognized for its specialized lubricants. Its products are designed to tackle the specific challenges of wind turbine operations:
- Reliability and Efficiency: Ensures continuous turbine performance, even in extreme conditions.
- Extended Component Lifespan: Reduces wear, maintenance frequency, and associated costs.
- Cost Savings: Minimizes downtime and operational expenses.
- Sustainability: Improves energy efficiency, aligning with global renewable energy goals.
Transform Your Wind Energy Operations
The success of wind energy depends on the optimal operation of turbines, and lubrication is critical to their longevity. MOLYKOTE® lubricants provide cutting-edge solutions tailored to the wind energy sector, offering peace of mind with products that are high-performing and environmentally friendly.
Explore our Wind Energy Market Page to see how MOLYKOTE® can revolutionize your maintenance strategy. Together, let’s power the future with efficient and sustainable wind energy.